Utilizing a pre-defined structure for troubleshooting documentation offers several advantages. Standardized procedures improve the speed and accuracy of repairs, minimizing operational disruptions. Clearly documented steps facilitate knowledge sharing and training for new personnel. A consistent format also simplifies the process of updating procedures as equipment or technology evolves, promoting best practices across an organization.
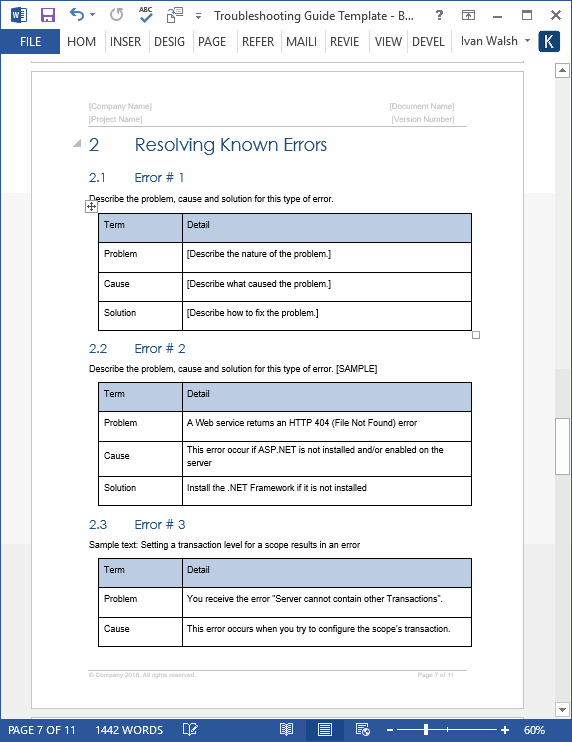
The following sections will delve into the key components of an effective framework for documenting troubleshooting procedures, including best practices for creation, implementation, and ongoing maintenance.
Key Components of a Troubleshooting Framework
Effective troubleshooting documentation requires a structured approach. Several key components contribute to a comprehensive and usable resource for addressing equipment malfunctions.
1: Problem Identification: This section clearly defines the observable symptoms of the malfunction. Precise descriptions, error codes, and visual indicators aid in accurate diagnosis.
2: Probable Causes: This component lists potential reasons for the observed problem, ranked from most to least likely. This prioritized list streamlines the diagnostic process.
3: Diagnostic Steps: A step-by-step guide outlines the procedures for investigating the potential causes. Clear instructions, safety precautions, and required tools are essential elements.
4: Recommended Solutions: This section details the corrective actions to address each identified cause. Specific instructions, diagrams, and part numbers facilitate effective repairs.
5: Verification Steps: Procedures to confirm the effectiveness of the implemented solution are outlined. This ensures the problem is fully resolved and prevents recurrence.
6: Escalation Procedures: Instructions on when and how to escalate the issue to higher-level support are crucial for complex or unresolved problems. Contact information and escalation criteria should be included.
7: Revision History: Maintaining a record of changes made to the document ensures accuracy and traceability. Dates, author, and descriptions of modifications should be documented.
A well-defined structure encompassing these components facilitates effective troubleshooting, minimizes downtime, and promotes consistent practices for maintaining equipment reliability.
How to Create a Machine Troubleshooting Guide Template
Creating a robust template ensures consistent and effective troubleshooting across an organization. A systematic approach facilitates development and implementation.
1: Define Scope: Specify the equipment or system the guide covers. Clearly define the intended audience and their technical skill level.
2: Establish a Standard Format: Choose a consistent structure for presenting information. This ensures uniformity and ease of use across multiple guides.
3: Develop a Template Structure: Incorporate the key components: problem identification, probable causes, diagnostic steps, recommended solutions, verification steps, escalation procedures, and revision history.
4: Populate the Template: Fill in the template with detailed information specific to the equipment or system. Include clear descriptions, diagrams, part numbers, and safety precautions.
5: Review and Validate: Subject the template to thorough review by experienced technicians and subject matter experts to ensure accuracy and completeness.
6: Implement and Train: Distribute the template to relevant personnel and provide training on its use. This ensures consistent application and maximizes effectiveness.
7: Maintain and Update: Regularly review and update the template to reflect changes in equipment, procedures, or best practices. Maintain a revision history to track modifications.
A systematic approach to template creation ensures a comprehensive and effective resource for troubleshooting equipment malfunctions. Consistent implementation and ongoing maintenance optimize performance and minimize downtime.
Effective equipment maintenance relies on systematic procedures for diagnosing and resolving malfunctions. A standardized framework for documenting troubleshooting processes promotes consistency, efficiency, and knowledge transfer within an organization. Key components such as clear problem descriptions, probable causes, diagnostic steps, and recommended solutions form the foundation of a useful resource. A well-designed template ensures these components are consistently applied, improving repair times and minimizing downtime. Regular review and updates maintain relevance and accuracy, contributing to overall operational efficiency and equipment reliability.
Proactive development and implementation of structured troubleshooting documentation represent a significant investment in operational excellence. This investment yields substantial returns through improved equipment uptime, reduced maintenance costs, and enhanced technician proficiency. Embracing a standardized approach to troubleshooting equips organizations with the tools and processes necessary to maintain equipment performance and achieve operational goals.