Utilizing such a framework can lead to faster repairs, reduced downtime, improved technician efficiency, and consistent documentation of troubleshooting processes. A well-designed structure also facilitates knowledge sharing and training for new personnel, contributing to a more skilled workforce and minimizing the impact of equipment failures on operations.
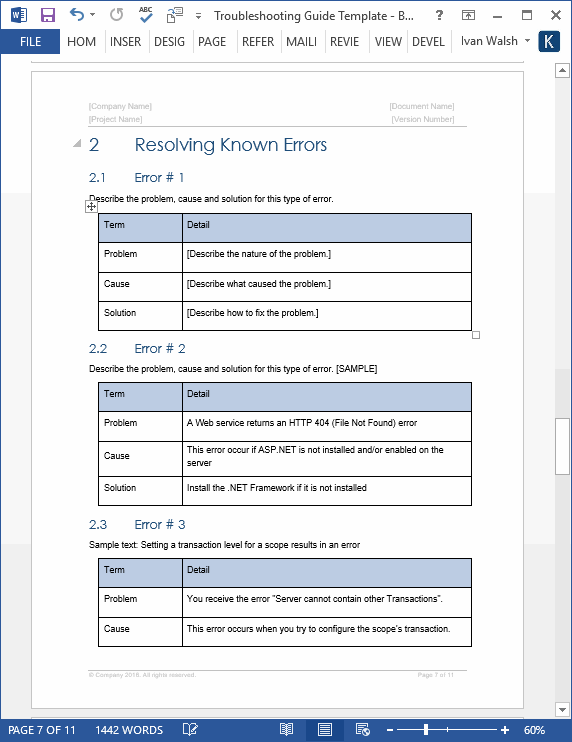
The following sections will delve into the key components of an effective structure for these documents, offering practical advice and examples for creating and implementing them within various operational contexts.
Key Components of an Effective Troubleshooting Framework
Effective troubleshooting frameworks rely on a structured approach to problem-solving. Several key components contribute to this structure, ensuring comprehensive and efficient resolution of equipment issues.
1. Problem Description: A clear and concise description of the observed malfunction is essential. This section should detail the specific symptoms, including error messages, unusual noises, or performance deviations. Objective details are crucial for accurate diagnosis.
2. Potential Causes: This section lists possible reasons for the described problem. Causes should be organized logically, perhaps from most likely to least likely, or categorized by system or component. This structured approach streamlines the diagnostic process.
3. Diagnostic Steps: A series of specific checks or tests designed to isolate the root cause. Each step should be clearly outlined, including the necessary tools, safety precautions, and expected results. Clear instructions minimize ambiguity and improve diagnostic accuracy.
4. Corrective Actions: Detailed instructions on how to rectify the identified problem. This section might include repair procedures, part replacement instructions, or software adjustments. Clear, step-by-step instructions ensure consistent and effective repairs.
5. Verification Steps: Procedures to confirm that the implemented corrective actions have successfully resolved the issue. This often involves repeating the initial tests or observations. Verification ensures the problem is fully addressed and prevents recurrence.
6. Documentation/Record Keeping: A designated space to record the troubleshooting process, including the observed problem, diagnostic steps taken, implemented solutions, and verification results. Thorough documentation facilitates future troubleshooting efforts and provides valuable data for preventative maintenance.
7. Safety Precautions: Clearly outlined safety procedures that must be followed throughout the troubleshooting process. This is critical for protecting personnel and preventing further damage to equipment. Safety should always be the paramount concern.
A well-defined structure, encompassing these components, provides a systematic and efficient approach to resolving equipment malfunctions, minimizing downtime, and promoting effective maintenance practices.
How to Create an Equipment Troubleshooting Guide Template
Creating a standardized template ensures consistent and effective troubleshooting across an organization. A well-defined template facilitates faster repairs, reduces downtime, and improves overall equipment maintenance.
1. Define Scope: Specify the equipment covered by the template. Clearly delineate the make, model, and any relevant variations. This ensures the guide’s applicability to the correct equipment.
2. Establish a Standardized Format: Adopt a consistent structure, including sections for problem description, potential causes, diagnostic steps, corrective actions, verification, and documentation. A uniform format promotes clarity and ease of use.
3. Develop Detailed Troubleshooting Steps: Outline specific procedures for each potential problem. Include clear instructions, necessary tools, safety precautions, and expected outcomes. Precision minimizes ambiguity and improves diagnostic accuracy.
4. Incorporate Visual Aids: Use diagrams, flowcharts, or images to enhance understanding and simplify complex procedures. Visual aids can significantly improve clarity, particularly for intricate tasks.
5. Implement Version Control: Establish a system for managing template revisions and updates. This ensures users are always referencing the most current information and reflects ongoing improvements in troubleshooting procedures.
6. Train Personnel: Provide comprehensive training on using the template effectively. This ensures consistent application and maximizes the benefits of a standardized approach.
7. Regularly Review and Update: Periodically review the template’s effectiveness and make necessary revisions based on user feedback and evolving equipment needs. A dynamic template remains relevant and valuable over time.
A well-structured, regularly updated template, combined with adequate personnel training, provides a powerful tool for managing equipment issues, leading to increased efficiency and minimized downtime.
Standardized documentation for addressing equipment malfunctions provides a systematic approach to problem-solving, leading to improved diagnostic accuracy, faster repairs, and reduced downtime. Key components of such documentation include detailed problem descriptions, potential causes, step-by-step diagnostic procedures, corrective actions, verification steps, and comprehensive record-keeping. A well-defined structure, combined with clear instructions and visual aids, ensures consistent application and facilitates effective knowledge transfer within organizations. Regular review and updates maintain the template’s relevance and effectiveness over time.
Effective management of equipment issues is crucial for operational efficiency and minimizing financial losses due to downtime. Implementing structured troubleshooting processes through standardized templates represents a proactive approach to maintenance, enabling organizations to address equipment malfunctions efficiently and systematically. This contributes to a more resilient operational environment and supports continuous improvement in maintenance practices.