Utilizing such a jig offers several advantages, including reduced errors, increased efficiency, and improved safety. By precisely controlling the drilling process, these tools minimize the risk of misaligned or incorrectly sized holes, reducing material waste and rework. Furthermore, they contribute to a safer work environment by providing a secure and stable platform for drilling operations.
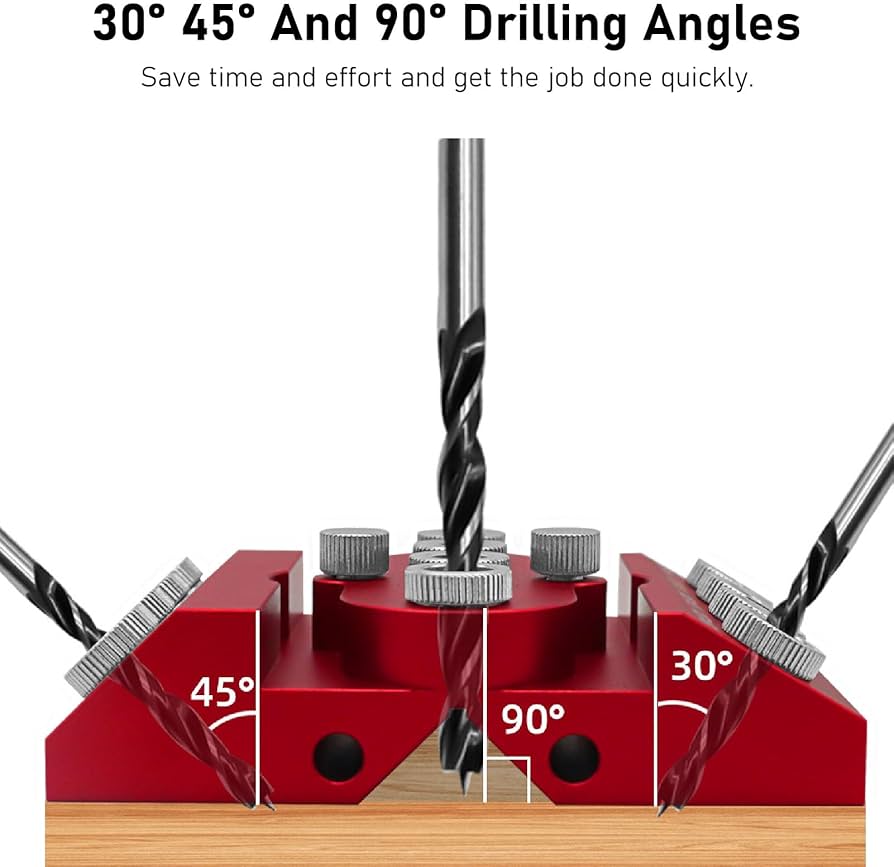
This introduction provides a foundational understanding of these essential tools. The following sections will explore the various types available, their applications in different industries, and best practices for their selection and use.
Key Components
Effective hole placement relies on several crucial components working in concert. Understanding these elements is essential for selecting and utilizing the correct tool for specific applications.
1: Base Material: The foundation of the jig determines its stability and durability. Common materials include acrylic, metal, or wood, each selected for its specific properties relevant to the application.
2: Guide Bushings: These hardened inserts precisely control the drill bit’s entry and path, ensuring consistent hole diameter and perpendicularity. Bushings are available in various sizes to accommodate different drill bit diameters.
3: Drill Bit Stop Collar: This component controls drilling depth, preventing over-penetration and ensuring uniform hole depth across multiple operations.
4: Clamping or Locating Features: These elements secure the jig to the workpiece, maintaining its position during drilling. These can include clamps, pins, or registration features that align with existing holes or edges on the workpiece.
5: Template Body: This is the main structure of the jig, holding the bushings and other components in the correct relative positions. Its design depends on the specific application and required hole pattern.
Careful consideration of these components, combined with an understanding of the specific drilling requirements, ensures accurate, repeatable results and optimal tool performance.
How to Create a Drill Hole Guide
Creating a custom drill guide requires careful planning and execution. The following steps outline the process for fabricating a jig for precise and repeatable drilling operations.
1: Material Selection: Choose a suitable base material based on the project requirements. Consider factors such as durability, stability, and ease of machining. Common materials include acrylic, hardwood, or metal.
2: Design and Layout: Accurately mark the desired hole locations on the chosen material. Utilize precise measuring tools and ensure proper spacing and alignment based on the project specifications. Double-check measurements to prevent errors.
3: Pilot Holes: Drill small pilot holes at the marked locations. These pilot holes guide the larger drill bit used for creating the final guide holes and prevent material splintering or wandering.
4: Guide Hole Drilling: Using a drill press or a hand drill with a drill press stand, carefully drill the final guide holes. Select a drill bit slightly larger than the intended drill bit to be used with the finished template. This allows for smooth passage of the drill bit during operation.
5: Bushing Installation (Optional): For enhanced durability and accuracy, install drill bushings into the guide holes. These bushings provide a hardened, wear-resistant surface and maintain consistent hole size.
6: Finishing: Deburr and smooth any sharp edges or imperfections on the template. This enhances safety and ensures smooth operation.
7: Testing & Refinement: Test the completed template on a scrap piece of material before using it on the final workpiece. Verify the accuracy of hole placement and make any necessary adjustments.
Precise fabrication and careful material selection ensure consistent and accurate results when using a custom-made drill guide.
Precise and consistent hole placement is critical in numerous applications, from woodworking and metal fabrication to electronics assembly. Employing a properly designed and fabricated jig ensures accuracy, repeatability, and efficiency in drilling operations. Careful consideration of material selection, guide bushing implementation, and accurate layout are fundamental to successful outcomes. This resource has explored the key components, construction methods, and advantages associated with these indispensable tools, providing a comprehensive overview of their significance in achieving precise and reliable drilling results.
As technology advances and precision requirements become increasingly stringent, the role of specialized tooling continues to grow. Continued exploration and refinement of drill guide technology will further enhance capabilities and enable even greater levels of accuracy and control in drilling processes. Investing time and resources in understanding and utilizing these essential tools empowers professionals to achieve superior results and maintain a competitive edge in their respective fields.